In today’s fast-paced industries, maintaining high-quality standards is more important than ever. One of the key tools that helps companies achieve this is NDT inspection. But what exactly is NDT inspection, and why is it so crucial for quality assurance? In this blog, we’ll explore the importance of NDT inspection, how it works, and the benefits it brings to various industries.
Understanding NDT Inspection
What is NDT Inspection?
NDT stands for Non-Destructive Testing. It is a method used to evaluate the properties of a material, component, or system without causing any damage. Unlike destructive testing, which can break or alter the item being tested, NDT allows for inspection while keeping the item intact and functional.
How NDT Differs from Other Testing Methods
Traditional testing methods often involve cutting, breaking, or altering the material to check its quality. NDT, on the other hand, uses techniques that do not harm the object. This means that NDT can be used repeatedly on the same item, making it a more efficient and cost-effective option for quality assurance.
Note – Ensure your quality assurance processes are in expert hands with top-tier NDT Inspection Dubai services from Raysun Techno Industries LLC. Discover how their advanced non-destructive testing solutions can enhance safety, reliability, and efficiency in your operations. Visit their website today to learn more and schedule a consultation, ensuring your projects meet the highest standards of quality and compliance.
The Role of NDT in Quality Assurance
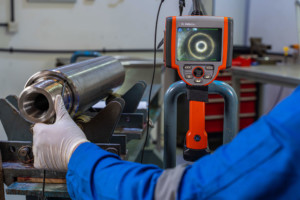
Ensuring Product Reliability
One of the main goals of quality assurance is to ensure that products are reliable and perform as expected. NDT inspection helps achieve this by detecting any flaws or weaknesses in materials before they become serious issues. By identifying problems early, companies can take corrective actions to prevent failures.
Preventing Defects and Failures
Defects in materials can lead to failures that may cause accidents, downtime, and financial losses. NDT inspection helps prevent these issues by thoroughly examining materials for any signs of defects. This proactive approach ensures that only high-quality products reach the market, enhancing the overall reputation of the company.
Enhancing Safety Standards
Safety is a top priority in many industries, especially those involving heavy machinery, aviation, and construction. NDT inspection plays a crucial role in maintaining safety standards by ensuring that all components meet the required specifications. This reduces the risk of accidents and ensures the safety of both workers and end-users.
Key Benefits of NDT Inspection for Quality Assurance
Cost-Effectiveness
Implementing NDT inspection can lead to significant cost savings. By detecting defects early, companies can avoid expensive repairs, recalls, and legal issues. Additionally, since NDT does not damage the product, there is no need to produce extra items for testing purposes.
Time Efficiency
NDT methods are often faster than traditional testing methods. This means that quality assurance processes can be completed more quickly, allowing companies to meet tight deadlines and maintain a steady production flow. Faster inspections also mean that any issues can be addressed promptly, minimizing delays in the production process.
Versatility Across Industries
NDT inspection is versatile and can be applied to a wide range of industries, including automotive, aerospace, manufacturing, oil and gas, and construction. Whether it’s checking for cracks in airplane wings or ensuring the integrity of pipelines, NDT methods can be adapted to suit different needs and materials.
Common Types of NDT Methods
Visual Inspection
Visual inspection is the most basic form of NDT. It involves examining the surface of a material or component for any visible defects such as cracks, corrosion, or misalignments. This method is simple, cost-effective, and often the first step in the inspection process.
Ultrasonic Testing
Ultrasonic testing uses high-frequency sound waves to detect internal flaws in materials. By sending sound waves into the material and analyzing the echoes, inspectors can identify cracks, voids, and other imperfections that are not visible on the surface.
Radiographic Testing
Radiographic testing involves using X-rays or gamma rays to create images of the internal structure of a material. This method is particularly useful for detecting hidden defects, such as voids or inclusions, within thick or complex components.
Magnetic Particle Testing
Magnetic particle testing is used to detect surface and near-surface defects in ferromagnetic materials. By applying a magnetic field and then introducing iron particles, any cracks or flaws become visible as the particles gather around them.
Liquid Penetrant Testing
Liquid penetrant testing involves applying a liquid dye to the surface of a material. The dye seeps into any cracks or defects, making them visible under ultraviolet or white light. This method is effective for detecting surface-level imperfections.
Implementing NDT Inspection in Your Quality Assurance Process
Choosing the Right NDT Method
Selecting the appropriate NDT method depends on several factors, including the type of material, the nature of the defects being sought, and the specific requirements of the industry. It’s important to evaluate each method’s strengths and limitations to determine the best fit for your quality assurance needs.
Training and Certification
Proper training and certification are essential for conducting NDT inspections effectively. Inspectors should be well-versed in the techniques and safety protocols associated with each NDT method. Investing in training ensures that inspections are accurate and reliable, leading to better quality assurance outcomes.
Integrating NDT into Existing Processes
Integrating NDT inspection into your current quality assurance processes requires careful planning. It’s important to establish clear procedures and protocols, ensuring that NDT methods complement other testing and inspection activities. This integration helps create a comprehensive quality assurance system that covers all aspects of product evaluation.
Case Studies: Success Stories of NDT in Quality Assurance
Example 1: Aviation Industry
In the aviation industry, safety is paramount. NDT inspection is used extensively to examine airplane parts for any signs of wear or damage. By regularly conducting NDT inspections, airlines can ensure that their aircraft are safe to fly, reducing the risk of accidents and maintaining passenger trust.
Example 2: Manufacturing Sector
In the manufacturing sector, maintaining high-quality standards is crucial for competitiveness. NDT inspection helps manufacturers detect defects early in the production process, allowing them to address issues before products reach the market. This not only improves product quality but also enhances customer satisfaction and loyalty.
Future of NDT Inspection in Quality Assurance
Technological Advancements
The field of NDT is continuously evolving with advancements in technology. Innovations such as digital imaging, automation, and artificial intelligence are making NDT inspections more accurate and efficient. These technologies are expected to further enhance the capabilities of NDT, making it an even more integral part of quality assurance.
Increasing Adoption Across Industries
As industries recognize the benefits of NDT inspection, its adoption is increasing globally. More companies are incorporating NDT methods into their quality assurance processes, leading to higher standards of product reliability and safety. This trend is likely to continue as the importance of quality assurance grows in a competitive market.
Conclusion
NDT inspection is a vital component of quality assurance, offering numerous benefits that help ensure product reliability, safety, and cost-effectiveness. By using non-destructive methods to detect defects and prevent failures, companies can maintain high-quality standards and meet the expectations of their customers. As technology continues to advance and industries increasingly adopt NDT practices, its role in quality assurance will only become more significant. If you’re looking to enhance your quality assurance processes, consider integrating NDT inspection to achieve better results and maintain a competitive edge.
For more insightful articles related to this topic, feel free to visit empireadda.com